THE BASIC TECHNIQUES FOR CASTING CONCRETE
Many people ask me questions about how I make my sculptures, so I thought I’d start a post about the process. I will update it from time to time so please leave all your thoughts and questions in the Comments section at the end.
Important disclaimer:
In no way I pretend to be an expert in concrete, as I have no special technical training in this area. What I’m sharing here is just the result of my own experimentations, done in a very empirical way with a trial-and-error methodology on how I cast concrete
So first, what is concrete? Concrete is basically a mixture of cement, sand, aggregates and water. Cement is one of the components of concrete and is not a synonym. That covers the basics, but since the concrete used by the Mayans, it has become a highly advanced material. Modern high-performance concretes have all kinds of additives that give it special characteristics, such as high density, fluidity, and fast curing.
Some artists make their own concrete mixes and I respect that a lot (Hi Balasz!). On my side, I decided to trust the big companies with whole engineering departments filled with very smart people, to do the job, so I just use pre-mixed concrete bags. Which one to choose, you may ask? Well, I will keep a trade secret here(…) but I’d suggest looking for something like a “countertop” mix. A mix that is well-balanced in terms of strength and fluidity.
Concrete is usually locally produced so I suggest you look at what brands they have in your local hardware store, write to the companies and ask for suggestions. That’s what I did and they were very helpful. Another reason why I don’t make my own mix is that every manipulation you make with cement powder generates a lot of very fine dust that can be very harmful for health over time. So I try to minimize it as much as I can.
SETUP
If you’re just starting, you’ll only need a bucket and a mixing tool; a small gardening shovel or a trowel works fine. As I just mentioned, dust is an issue, so if you can, work outside. If, like me, you’re stuck inside, try to keep the dust confined, as it can be a pain to clean if it gets everywhere. In my first studio I made some kind of tent with plastic sheets. Better than nothing but not that great.
This very simple DIY filtering system looks very bad but works pretty great. I took an old (toilet) cardboard box and hooked on top my workshop vaccum, equipped with HEPA filters for fine particles. It creates a negative pressure area that keeps the dust relatively contained.
Mixing
Now, follow the instructions on the bag; the water-to-powder ratio will be mentioned.
Stick to the ratio! I know, you’ll be tempted to add more water to make the mix more fluid and get better details. If the mix is too stiff, try mixing longer. If it doesn’t work, get another mix. Too much water weakens the concrete, making it more brittle and prone to cracking. Be aware that cracking may occur several weeks or even months after the piece is unmolded.
Once you have carefully weighed your water and concrete, put about nine-tenths of the water in the bucket and gradually add the concrete while stirring. I really like this analog scale as it doesn’t always resets after a few seconds if you’re not fast enough. Plus it never runs out of batteries! Adjust with the remaining water one drop at a time until you reach the desired consistency. It’s always easier to add more water than adding extra concrete to adjust the fluidity.
Note: I have found that with the mix I use, there can sometimes be a bit more aggregates at the bottom of the bags. Therefore, I try to mix the entire bag as much as possible. Additionally, I hate weighing small quantities of concrete powder, so this saves me that step.

Try mixing the whole bag
If you’re mixing whole bags or getting into it a lot, I highly recommend using a drill equipped with a mixing paddle. It will save you time, hassle, and produce a better mix. Make sure to mix enough, but don’t overmix (it should be part of the instructions on the bags). Over-mixing can introduce too much air, resulting in air pockets in your mold and a faster setting time, giving you less working time.
When you have finished mixing, look for bubbles rising at the surface; a few bubbles is normal. If you see a lot, wait a minute or two and gently remix. In my experience, a lot of bubbles is often a sign that you have used too much water.
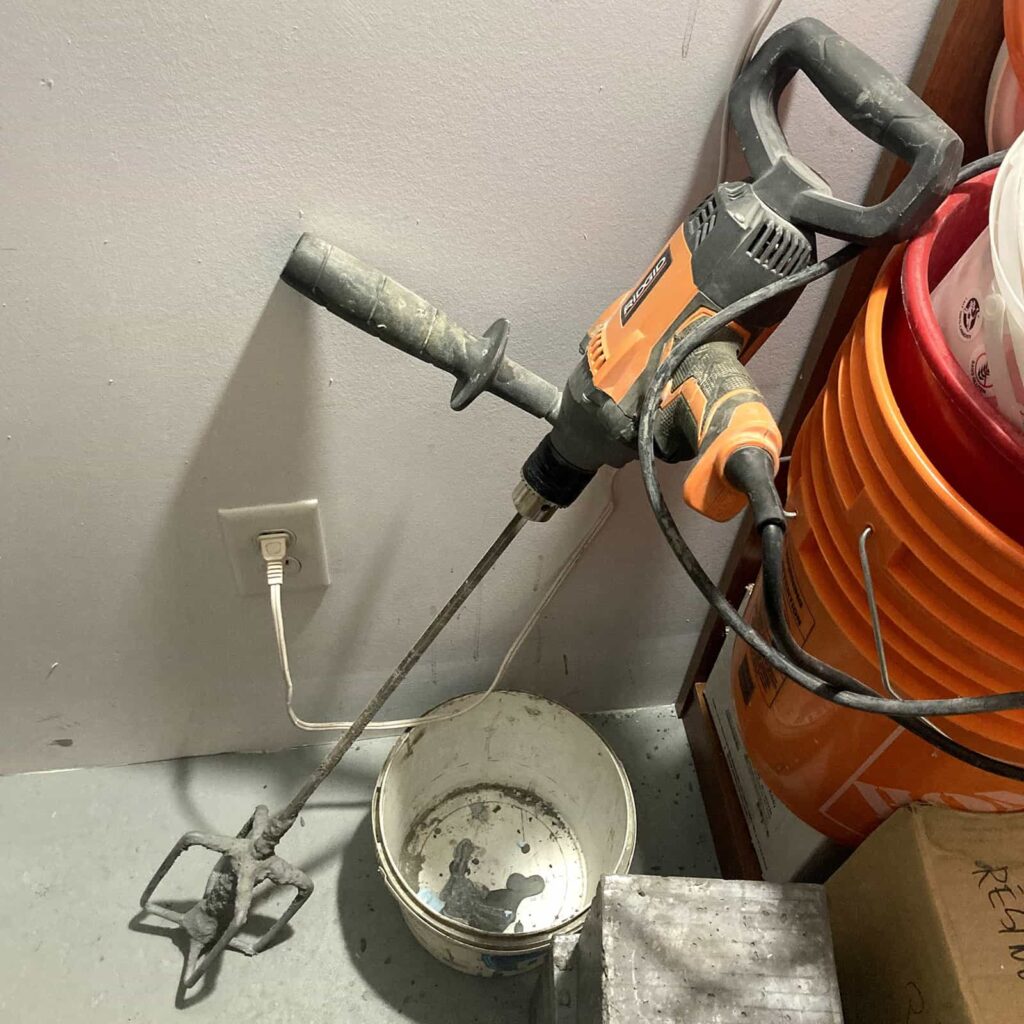
Pouring
The principle is the same as with any casting: pour the concrete starting from the lower point of the mold. Ideally, the concrete should flow in the mold, starting on one side, reaching the bottom, and coming up on the other side in a circular motion. This really helps to prevent air from getting trapped.
At this stage, you’ll probably want to shake the mold to help the concrete settle evenly. As with everything, a little bit is good, but not too much. For large pieces, weighing 15+ kg, I usually just shake the mold a little bit, balancing it from side to side. For smaller pieces, I sometimes vibrate them using a handheld massager for 15-20 seconds. I borrowed this one from my stepfather many years ago, I hope he is not reading this post… Too much vibration can release air bubbles that can create holes in the surface and separate the aggregates and the water (that’s bad)
I usually find that casting large pieces is easier than small ones, as concrete takes advantage of its own weight and spreads more easily in the mold, thus requiring less shaking and vibrating. The openings in the molds where the concrete can be poured are usually larger, making them easier to fill.
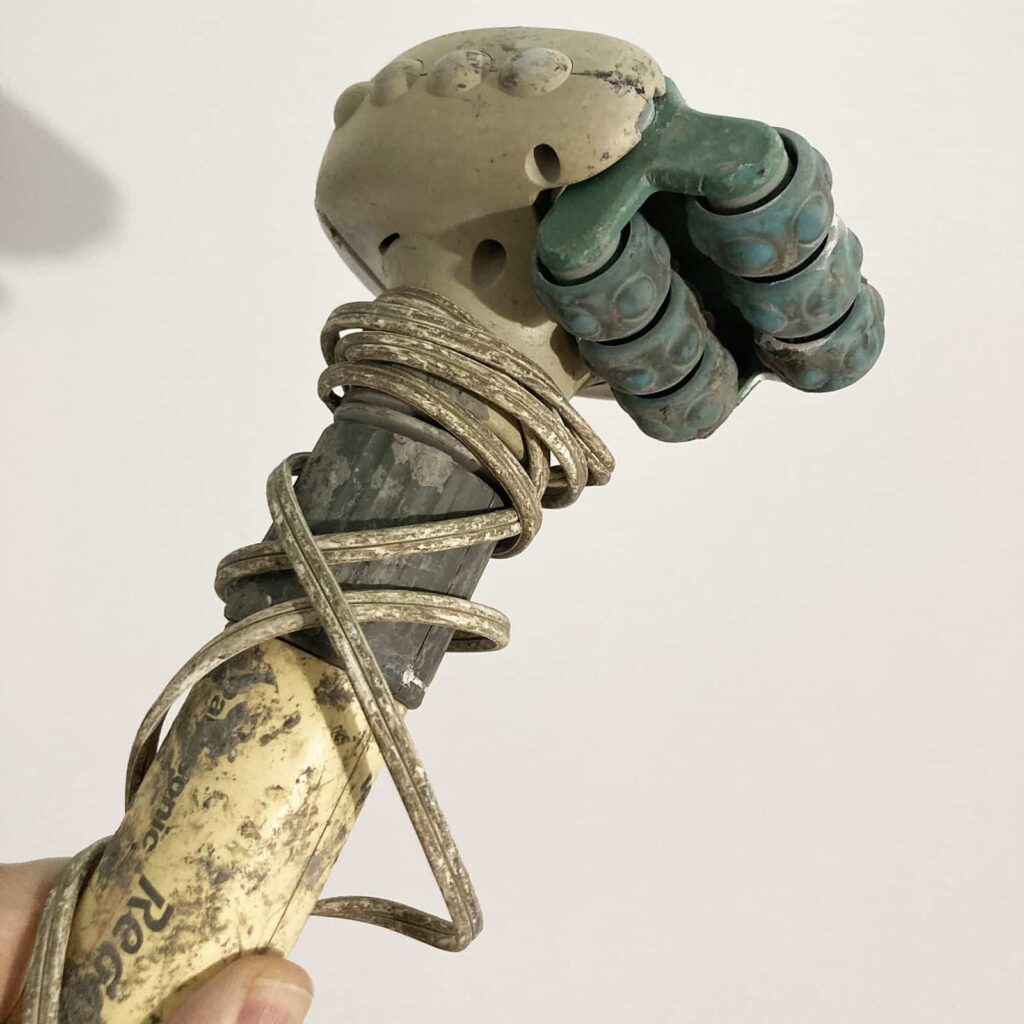
Unmolding
The curing period before you can unmold depends on the mix (real label…). It can also greatly be affected by the environment conditions. Warm temperature = faster curing time. Humidity is you friend. Concrete cures best in humid conditions. With the mix I use, my ideal curing time is two to three days. You can leave it in the mold for as long as you want, but if you unmold it too early, it will be weak and brittle. It can also lead to cracking that can occur a few days, weeks, or even months later. (I said it before, but cracking is my worst nightmare, so I’ll say it again)
The complete curing period for most concretes is 28 days. It follows a logarithmic curve, so after a few days it will have almost reached its maximum strength, and will continue to improve over the next few weeks.
Note: We often say that we let the concrete dry, which is not entirely true. Concrete does dry, but it mostly cures. Water reacts chemically and does not evaporate as much.
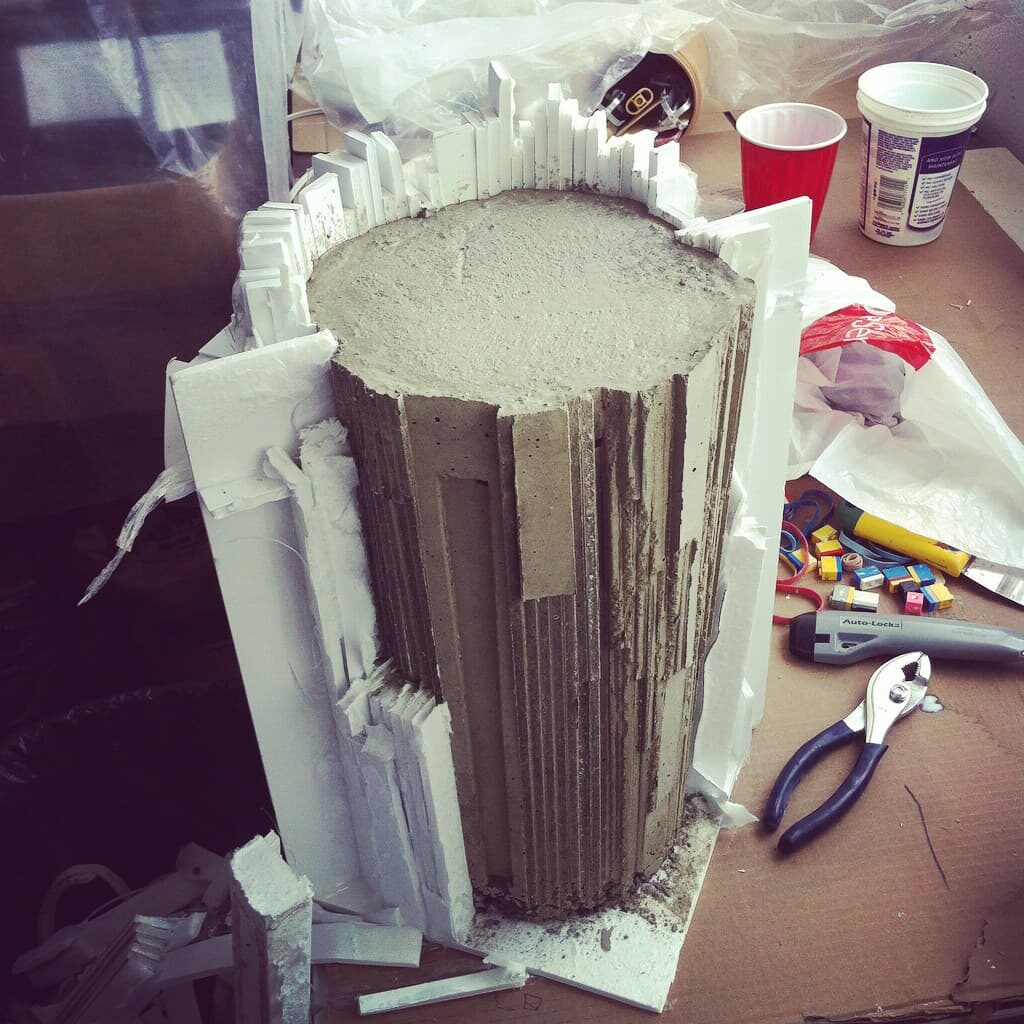
Finishing
Because of the aggregates, I try as much as possible to avoid sanding or polishing. These actions will eventually reveal the aggregates that are usually stronger that the cement mix and of different color. Unless you want a terrazzo-like effect. I usually just buff the ragged or sharp edges with a file or sand paper.
The last step is to wash it under running water to remove all the dirt and dust. Then, I usually wipe it dry with a cloth, as water puddles can leave stains. Voilà!
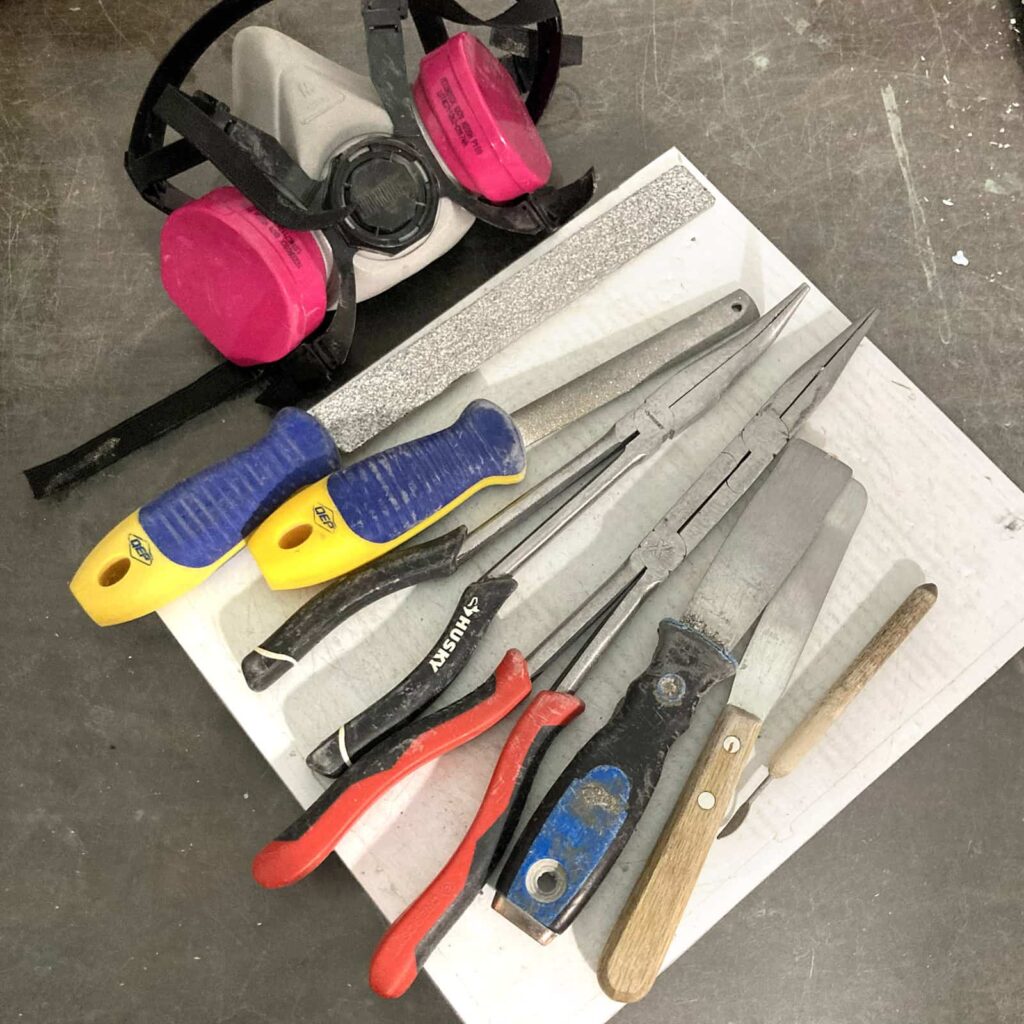
27 Responses
Very cool!
Thanks Nathalie
Thanks you for this!! I really love your work, and the fact that you share your knowledge with us is amazing. Much love
My pleasure Laura !
Thank you very much for sharing your knowledge.
You’re very welcome Keter !
Thanks so much for sharing.
What material do you prefer for a mold?
Hi Ezra,
These days I mostly use extrude polystyrene, but I may get back to urethane rubber.
I’ll make a few posts about my molds in the upcoming weeks. Stay tuned
Best
Hi David,
Thank you for sharing!!
Have you ever used jesmonite for casting?
And do you need any reinforcement for the concrete casting?
Best,
Yuval
Ohh, just googled Jesmonite, didn’t know about it. I might have to try it, thanks for the tip!
As for reinforcement, not at the scale I’m working.
Thanks Yuval
Amazing! Thanks so much for your tutorial!!
What type of concrete do you use, is there a specific brand or product that results in the smooth finishes that you get?
Thanks,
Jason
Hi Jason, I really like SIKA brand.
I’ve tried a few products and I mostly use their self compacting concrete mixes. Cheers
Hi David,
Thank you for sharing and I find your work inspiring. I’m a research student doing my MA in Fine Art. Do you use an eco brand concrete mix, as sustainability is a big topic?
Regards
Blair
Hi Blair, thank you very much! I am not aware of eco-friendly brands (in Canada), but I’d definitely switch if I had the option. If you find any please share it here! All the best
Hello David
Thank you very much for sharing your concrete casting . I’m really enjoying following your wonderful work on ig. As a maker myself it’s great to see a little bit behind the scenes. I work with glass casting and I love the idea of combining glass with concrete. I tried a couple of tiny casts in concrete left over from making the plinth for my workshop. Reading what you’ve shared inspires me to have another go! Many thanks Angela
Hi Angela, thank you very much for your feedback, it’s really appreciated! I have just looked at your work http://www.angelathwaites.com
It’s beautiful. I myself tried a glass casting class a few years ago and it was one of my most exciting (and scary) art experimentation. Scooping magma with a big spoon in sand molds was definitely out of my comfort zone. Glass by nature is made of sand so I find there’s a very natural connexion between concrete and glass. I’ll make sure to follow your journey in arts. All the best
Hi, David.
Thank you so much for sharing your process, and (as I read in the comments) for what you are going to share in the near future.
I have two questions.
¿Do you apply some sort of de-molder to make your unmolding easier? If you do ¿which one do you use?
¿How do you cut the extruded polystyrene?
All the best from Mexico City
Hi Fernando, thanks for reading and for your questions, I really appreciate! Extruded polystyrene doesn’t stick too much so I don’t use demolder, although I should probably do… I have tried a few times using cooking spray oil (in aerosol cans) and it worked pretty good. I think I’ll try again on my next piece.
And to cut the polystyrene, I use a hotwire table.
All the best from Montreal !
Hi David,
Thank you for sharing your methods.
Plumbing wise what are your steps to avoid blockages or accumulation of sediment from clean-up? 🪣
Thanks!
Hi Magdala, that’s a very good question, I’ll add a note in the post. Don’t throw any residue in the plumbing as it will indeed eventually clog your pipes. I clean my buckets with as little water as possible, tranfer the water and the sediments in another bucket an let the water evaporate. Then I dispose of it as any dry waste. Cheers!
It’s interesting to know that concrete would be produced locally most of the time, and we should check the brands available in our area as well as ask for suggestions from sellers. My husband said that we might need to get pre-mixed concrete for the construction of our driveway once we hire a contractor. It would be a good idea to know how much they would cost so that we can prepare our budget.
Hi David,
Love your work! Very inspiring. I’m currently hoping to cast a mini maze sculpture in concrete and with this being my first time using the material, the information you’ve shared is extremely helpful. I have a couple of wee questions about your process:
– How do you attach the pieces of extruded polystyrene to each other to create the mould?
– Are there any alternatives to a hot wire table you might recommend for cutting the extruded polystyrene?
Many Thanks from Scotland!
Hi Eilidh, I’m happy to hear this information was helpful!
-To attach the pieces together, I use hot glue
-To cut polystyrene, I also very often use a box cutter. Just don’t be cheap with you blades and change them frequently.
Good luck with your project and feel free to share a few pictures here when it’s done
Thank you for sharing your valuable information!
If I may ask a question
– how can the resultant concrete finish be a little bit shiny/glossy to look at?
Thank you
Hi Tejas,
I’m so sorry, for this very very late reply, I missed your message.
Concrete really takes the texture and finish from the mould, so if your mould is glossy, your finished piece should also be glossy.
Thanks!
Hi David,
Thanks for this post!
I recently did my own concrete pour using syka concrete, at a very similar scale to some of your own, yet my pour came out with an unseemly gradient to it? The bottom of some of my objects were grainy and not properly set, with a dark grey look to it, they would deteriorate when I touched them, yet the top of my pours had a nice smooth finish. Would you happen to know why?
The pour was done in an extruded polystyrene mould.
Thanks!
Hi John, thanks for your message.
I’m not a technical expert but from my experience, when concrete crumbles it’s usually when there was too much water in the mix.
In your case, since there is a demarcation, is it possible you shaked it a lot?
Best
David